How Marty Maslen’s Passion for Codes and Off-Site Construction Shaped Her Career, Brought Her Back From Retirement
Maslen, a Colorado code official with extensive experience in off-site construction, is well-versed in its many benefits when compared to traditional stick-built methods for both commercial and residential properties.
Off-site construction has been growing for years, but recent events – including supply chain challenges and an ongoing labor shortage – have increased interest from builders and manufacturers. The National Association of Home Builders has shared multiple accounts of why the home building industry is looking to go off-site, including reduced fuel and shipping expenses. In addition to the potential cost savings, a report by McKinsey shows that modular construction accelerates project timelines by as much as 50 percent.
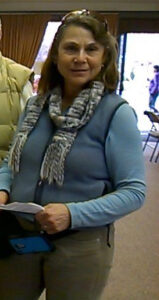
Marty Maslen, a Colorado code official with extensive experience in off-site construction, is well-versed in its many benefits when compared to traditional stick-built methods for both commercial and residential properties. In particular, she said that schools have taken advantage of modular builds to handle extra overflows when they can’t immediately expand beyond their existing walls.
See Related: What is Off-Site Construction? Solutions for Today’s Challenges
“The whole other kettle of fish is how important it is to verify that it is put together correctly,” said Maslen. She cited one of the key challenges for off-site construction: ensuring that each piece is structurally sound from the day it leaves the factory to the moment it arrives at its final destination. Potholes and other road hazards must be factored in. But the factory setting has provided an environmentally friendly way to reduce the risks incurred during transport.
“They can reuse every piece of scrap until there’s next to nothing left,” Maslen explained. “In stick-built construction, leftover pieces of Sheetrock have no use. In the modular world, they can take those pieces and glue them on the horizontal seams so they won’t fracture going down the interstate.”
This may reduce the need for future repairs and lower the overall cost of construction. The fees associated with transporting tools and talent may also be reduced. Instead of having to pack up and move to different locations, off-site construction allows everyone to work in one place that’s protected from the outdoor elements.
“Now they can provide more value than they would if it was done in the stick-built world,” said Maslen.
Off-Site Construction has Many Advantages, but Stick-Built Homes aren’t Going Anywhere
Another advantage of off-site construction is the speed with which new homes can be deployed following a natural disaster. Colorado has endured several disasters in recent years, including fires and a statewide flood that damaged or destroyed more than 26,000 homes. Two hundred businesses were also destroyed and 750 were damaged. By developing modular structures off-site, Maslen said that builders can replace damaged or destroyed properties at a much faster rate than would ever be possible with traditional on-site construction.
That said, Maslen does not expect stick-built homes to disappear. For some cities, stick-built is simply the mainstay. In other instances, builders may not have the capital to invest in the necessary equipment to build off-site or manufacturing capacity doesn’t exist in the region. Builders may also prefer to proceed with a process they are familiar with, even as supply chain woes encroach on profit margins.
“The nice part about a stick-built home is that the homeowner can walk the house,” said Maslen. “If they don’t like something, they can change it while it’s in process. It could be something as simple as an incorrect counter height, or maybe the cabinets are too far out of reach. In the modular world, people don’t usually get to see their house along the way.”
A Lifelong Passion for Codes and Off-Site Construction
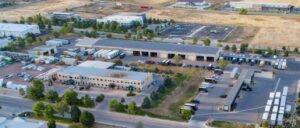
Maslen’s career as a code official began when she was looking for a job to help provide for her family. One of her classmates from high school had become a builder, so she decided to pick his brain about what that entailed.
“He thought I’d be really good at codes,” she recalled. “I went off someone else’s judgment, and I enjoyed it to no end.”
Her profession quickly turned into her passion as she dove into its inner workings. She relished the opportunity to learn and would immediately take a test as soon as she completed each codebook. By 1993, Maslen was out in the field as an inspector.
“There are a lot of ways to get into this profession compared to when I started,” said Maslen, adding that a growing number of community colleges are expanding their curriculum. High schools are starting to do the same. This will go a long way toward expanding the industry to become more diverse and inclusive.
“It’s good to have a full cross-section, whether we have people coming out of the trades or people who have never touched a tool in their life,” she affirmed. “I think we all bring an important piece of how to see things.”
Returning With an Excitement for “Talking Code”
After roughly 30 years, Maslen thought she was ready to retire from her career as a Colorado code official. But her love of the job, which allowed her to regularly share her knowledge and expertise, made it impossible for her to give up her work entirely. She missed the day-to-day interactions with builders and homeowners, and she especially missed “talking code” and explaining why a particular code matters.
“The energy code is a great example, and the International Code Council has been a great educator for it,” said Maslen. “That’s one of the newer ones we’re trying to convey to customers, why they should be doing this. It can reduce energy consumption in every commercial and residential building.” And that includes both off- and on-site construction.
See Related: Navigating the Tiny Home Landscape
Maslen, a certified full combination building inspector involved in plumbing, mechanical and structural, ended her retirement to serve as a part-time inspector for the city of Longmont, Colorado. Her experience with the energy code dates back to the early 2000s when she worked with the Code Council’s Colorado Chapter, which connected her with its mentorship program to help tradespeople become inspectors. One of her mentees went on to become an inspector for the city of Greeley; another serves as an inspector for the city of Loveland.
“The Code Council is an organization that helps all of us be organized,” said Maslen. “When I stepped out and became a building official, I relied upon both the Colorado Chapter and the Code Council for interpretations, which was prior to commentaries being issued by the Code Council.”
Whenever she needed guidance, Maslen turned to Becky Baker, a Master Code Professional, former president of the Colorado Chapter and director of building safety for Jefferson County. She also drew upon the expertise of Mike Gebo, as well as Bryon Horgen.
“The nice part is they help guide us and help each of the committees set up all these codes, which are updated every three years,” she said. “It’s kind of like a family tree – it just keeps branching out.”
Whether Off-Site or On-Site, Maslen Truly Loves Her Work
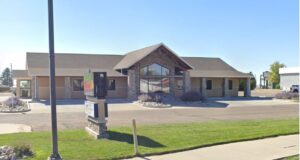
As an inspector, Maslen’s day begins with her inspection workload, followed by an outline to guide how to best complete her workload, as well as any timelines that may have to be met. Anything and everything can and will influence her schedule when performing inspections, which can quickly pivot from an eight-hour timetable to an exhausting 14-hour shift.
Maslen’s schedule also depends on the schedules of each contractor. If anyone is ahead or behind, someone will end up waiting, and it can quickly create a chain reaction that leads to further delays for all parties.
“Sometimes the subcontractors would get out of line of each other,” she said. “Who comes in first and who’s on last? If that gets out of sequence, they have to figure out how to get around things that are not normally in their way.”
Despite the obstacles, Maslen truly loves her work. She takes satisfaction in the end result – being able to see the building in front of her, knowing that she played a part in the project’s health and safety. She is especially excited by assignments that challenge her, including the many pieces of code that factor into commercial properties, and she has fond memories of a project involving a custom home.
“He was a homeowner from Germany, he built his own home and he stick-built his own hip roof,” she said. “It was the first time I had seen such a complexity put together without it being engineered.”
Now Maslen is primarily focused on her new role with the city of Longmont.
“I really like how my current employer presents themselves – as an advocate that’s here for consultations, here for answering questions, and not just about code enforcement,” she concluded. “No one knows everything about every code. It’s a huge amount of information, and we can all learn and rely upon each other. That’s why I like sharing my knowledge.”