Amazon’s Second Headquarters Highlights Water Reuse and Code Safety in Arlington, Virginia
Amazon’s second headquarters was built from the ground up to provide a green working environment, and that includes one of Virginia’s most extensive water reuse systems.
Amazon had ambitious plans for its second headquarters in Arlington, Virginia. Known as HQ2, the company wanted to build Metropolitan (Met) Park to be an incredibly sustainable campus with zero operational carbon emissions. It also strived for LEED Platinum certification and, as a result, recently became the world’s largest LEED v4 project for Building Design and Construction.
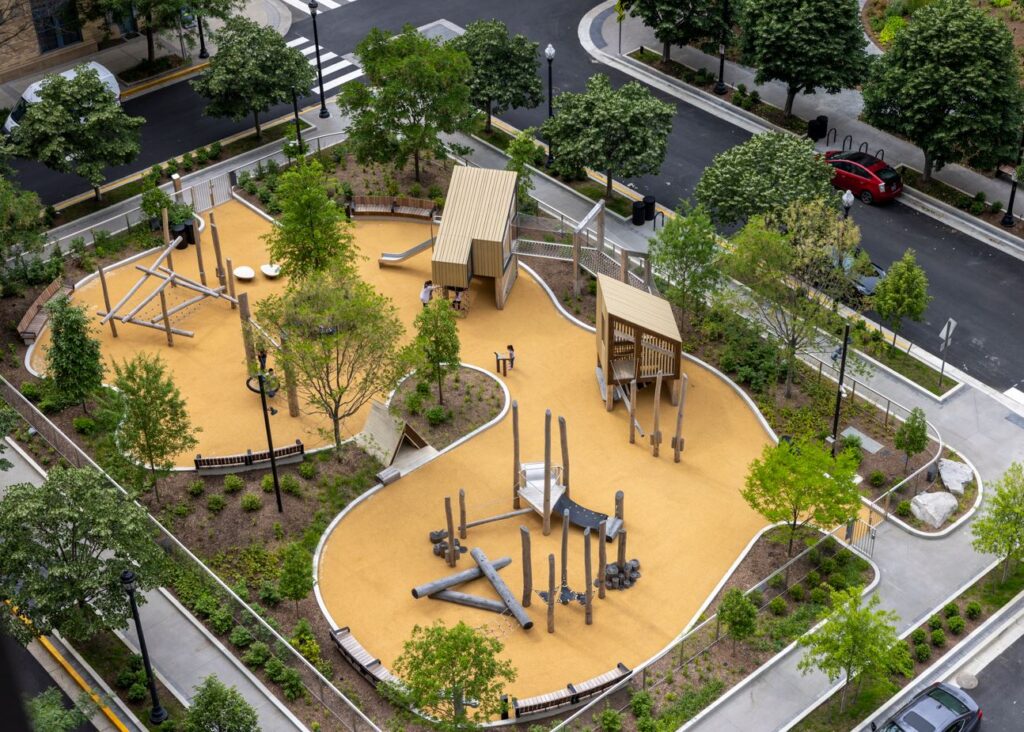
Better still, Amazon saved more than 14,700 metric tons of carbon (the equivalent of the carbon produced by 3,200+ cars annually) through a 20 percent reduction in the carbon footprint of Met Park’s concrete structures.
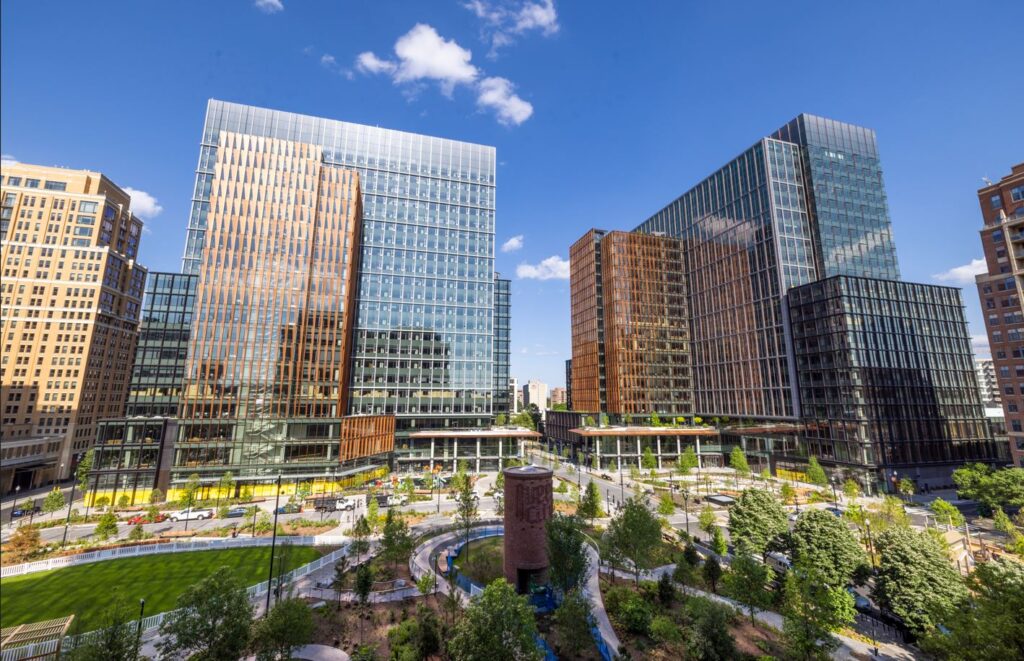
These efforts have made HQ2 one of the greenest campuses in the country, but Amazon didn’t stop there. The company worked with building safety professionals in Arlington to reduce water consumption by reusing water and reducing consumption. From low-flow urinals, toilets and lavatories (which exceed EPA requirements by nearly a third) to low-flow irrigation that hydrates native plants without wasting water, HQ2 is committed to conservation. Read how an elementary school in Wimberley, Texas, set a similar goal to improve water conservation.
“[Amazon installed a] massive water reuse system,” said Shahriar Amiri, Chief Building Official, Inspection Services Director at Arlington County, Virginia. “Primarily they’re using either greywater or recycled water for all their irrigation systems. They’re using it for all their toilets, urinals and their cooling towers.”
The project sometimes required not one, but two building inspectors working full eight-hour shifts over two weeks to make sure that every component was up to code.
“It was a complicated project,” Amiri continued. “I think what helped is that we had a lot of consultation meetings and we, as building safety professionals, learned from the things that designers do. It’s not always that way. But there are things we see in the building system or processes, like this water [collection and reuse] system, that we haven’t seen before. It was one of many firsts we saw in this building.”
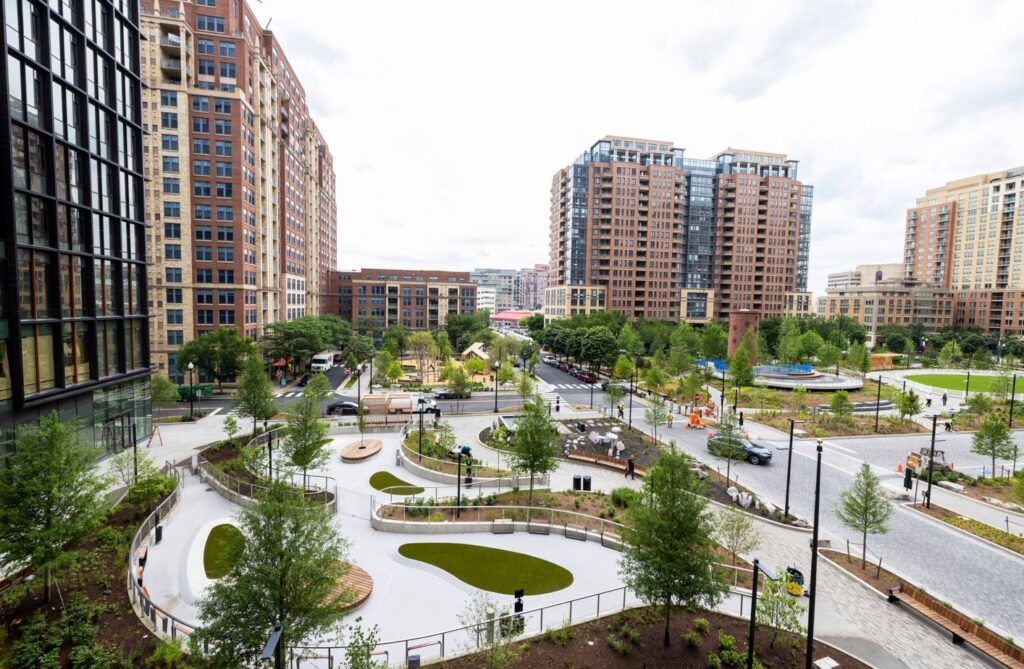
How Amazon’s HQ2 Will Recycle Millions of Gallons Every Year
Virginia has adopted the International Code Council’s International Codes® (I-Codes) and intends to uphold this adoption indefinitely, tailoring any amendments to suit the specific requirements of the state. For all practical purposes, Amiri said that HQ2 was built in accordance with the International Plumbing Code® (IPC). Read how the I-Codes are paving the way for more resilient communities.
“That’s the standard,” Amiri explained. “With the Code Council, we are always trying to keep up with the industry. Chapter 13 of the IPC deals with non-potable water systems and Chapter 14 deals with subsurface landscape irrigation systems. That was the basis of our plan review and system inspection. All the testing and requirements, everything.”
The list of requirements was too big for Amiri to cover in full, but he mentioned the control valve, sizing and signage. That latter aspect requires all sources of non-potable water to be marked with “do not drink” notices, even if the water comes from a urinal or another source that people aren’t likely to consume.
HQ2 captures three forms of water for non-potable reuse: rainwater, shower water and HVAC condensate. The tanks had to be tested quite significantly due to their location, size and use to ensure that the proper backflow preventions were in place and that all the code requirements were met. Amiri noted that the plumbing code has very specific requirements for non-potable water use and that this project took advantage of all of them.
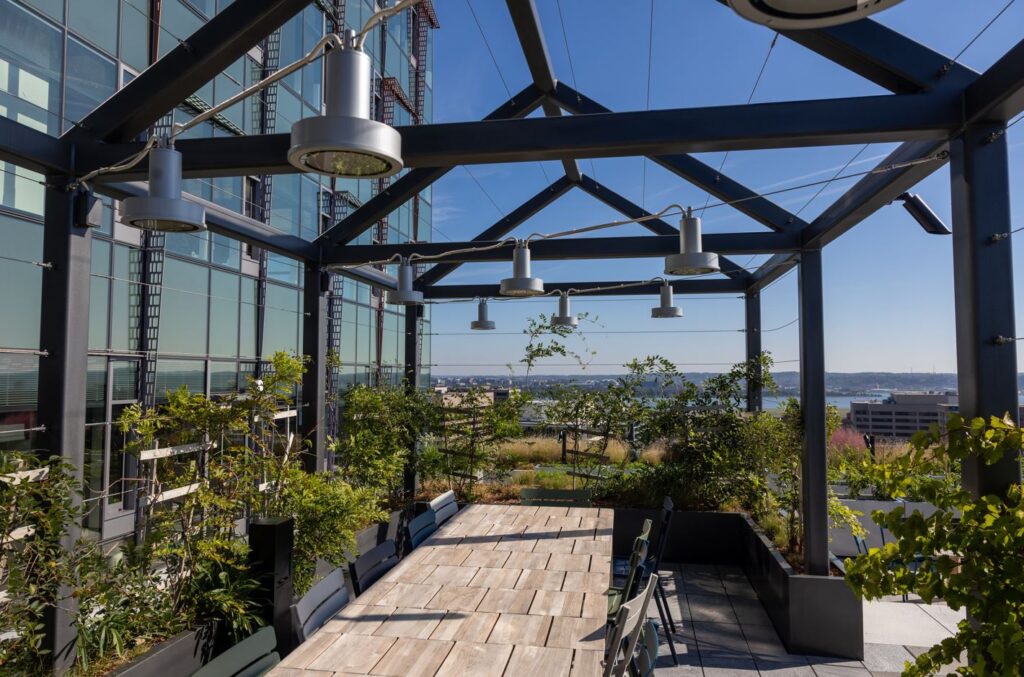
“It was a learning experience,” he said. “It’s not like we see a building like this every day. You see [non-potable water use] in very small applications, but in this state, we haven’t seen it very often.”
Amazon intends to recycle 7.5 million gallons per year – more than enough to fill the Lincoln Memorial reflecting pool. If successful, HQ2’s water savings could be 50 percent below what is required by the code.
Once collected, the water must be treated and stored deep underground. Large bodies of water are vulnerable to flying insects and other vermin that could contaminate the reclaimed H2O, spread germs and make people sick.
“I’ve been in this business 37 years and counting,” said Amiri. “I’ve been a building official for major jurisdictions, but the buildings that come to Arlington are different. Because land is sparse, they go up and below grade. There is no surface parking anywhere in Arlington, so everything gets buried within the building, including these types of [water storage] systems.”
While many water reuse systems rely on tanks that store water outside, Arlington is too cramped to allow for a similar setup.
“Everything needs to intermix with all kinds of parking, the piping system and wiring inside the building,” Amiri added. “That’s what makes it complex because it’s not some [flat] building. It’s not like a warehouse with a water reclaim system. You’re dealing with a 26-story building [with a parking garage that’s] three or four stories below grade.”
Water Reuse Systems in Amazon’s HQ2 Presented Building Safety Challenges Rarely Seen in Arlington
Arlington County building safety professionals worked tirelessly to inspect every part of HQ2. They took special care to make sure that the different systems (in terms of backflow preventers and varying water supplies) did not cross. Any mistake could lead to contamination and create unnecessary waste in a facility that was built to be as efficient as possible.
“It’s one thing doing it on plans,” said Amiri. “Plans always get it right. But when the plumber is piping it, there’s quite a probability that they’ll cross pipes. And that’s where it comes to the intense part of the conversation: to make sure they don’t cross each other. Then they’d end up with contaminated water. Cross-contamination is a major part of the plumbing code.”
Amiri’s inspectors ultimately chose to inspect by section to prevent any confusion while working on such a sizable building.
“You can see the massiveness of the facility,” said Amiri. “The electrical switch room looks like three or four basketball courts. You can’t see the end of it when you open the door – it’s that huge!”
Though the size was significant, building safety professionals will likely remember HQ2 for its extensive use of the IPC.
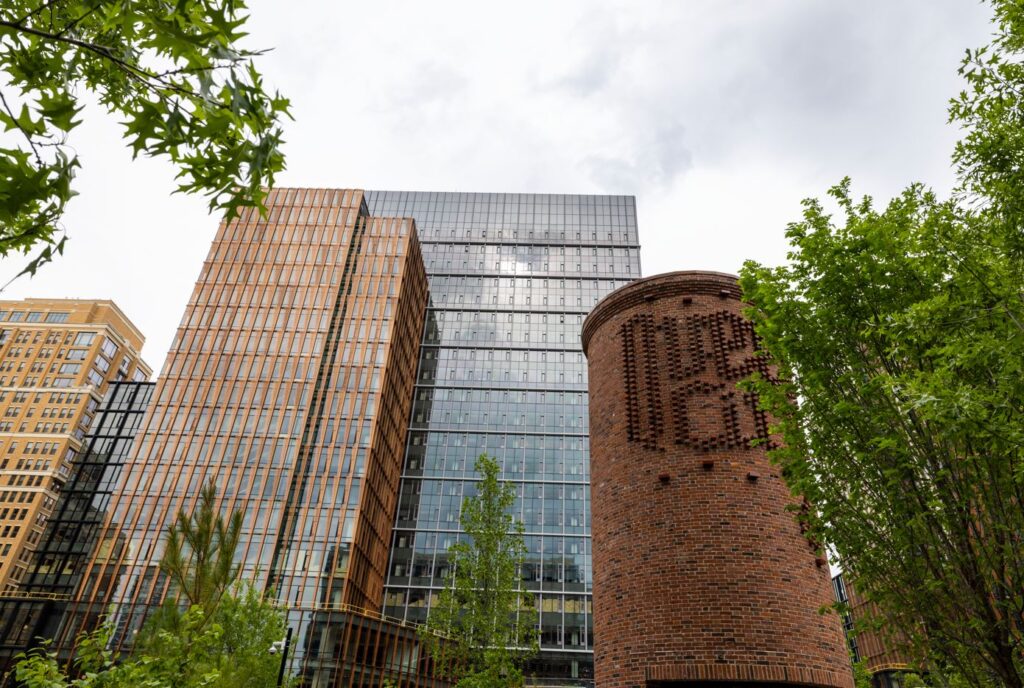
“It’s not too often we use all provisions of the code,” Amiri concluded. “Especially a provision for greywater, irrigation or rainwater. I think we used the codes from end to end when it came to this.”
Learn more about the Code Council’s plumbing, mechanical, fuel gas, swimming pool and spa, and private sewage disposal codes here.